2000年頃までの国産自動車は、加速性能や回転のスムーズさを求めて多気筒化が主流だった。しかし時代が変わって環境負荷の低減が主題に移った今は、熱効率の追求やモーターのアシストなどの影響でエンジンの気筒数は減少の傾向にある。
その中で、1600ccあたりまでの小排気量エンジンの主流となりつつあるのが直列3気筒である。ここでは、直列3気筒エンジンのメリットとデメリットについて詳しく解説する。
直列3気筒を採用する5つの理由
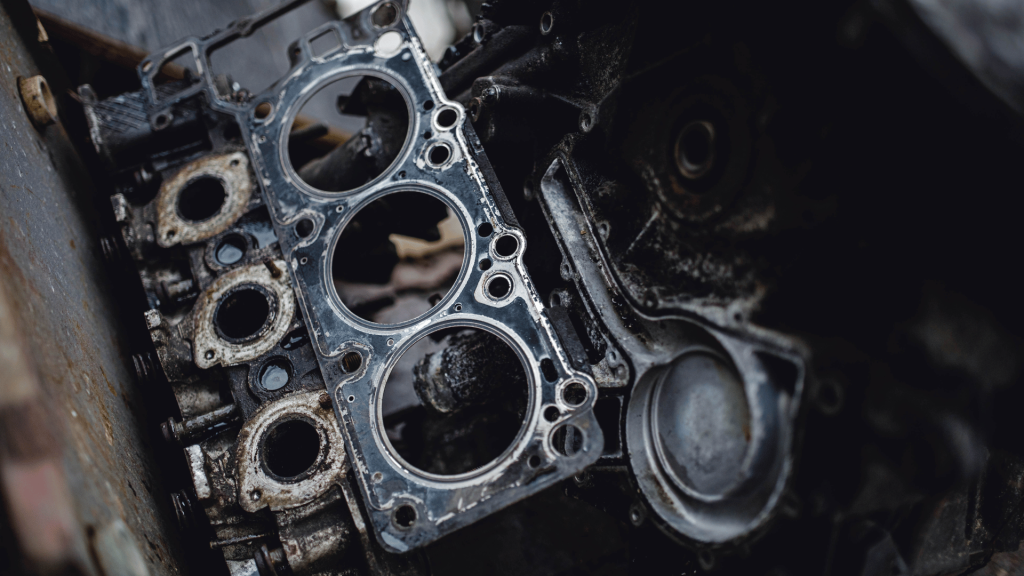
では、直列3気筒エンジンを採用する主な理由について説明する。
生産効率を向上させるモジュール化が活用できる
メリットのひとつ目は、生産効率の向上が見込めるという点。レシプロエンジンの排気量は、1気筒あたり400〜600ccが目安とされている。これは、得られる出力に対するフリクションや熱損失などのロスの比率が最も少ないとされることや、エンジンのサイズとボア×ストロークのバランスなどの要素を考慮したもの。
その数値を踏まえると、4気筒なら1600〜2400cc、6気筒なら2400cc〜3600ccとなり、ほとんどのエンジンはその範囲に収まっていることが分かる。そしてこのことは、エンジンの排気量のバリエーションを作る際にも応用できる。
例えば直列4気筒エンジンを設計するとして、排気量を1600ccに設定した場合、そこから1気筒を減らすことで、1200ccの直列3気筒エンジンを派生させることができる。
これには内部の稼働部品を共用できるという大きなメリットがあり、設計コストも生産コストも大きく削減できる。
機械的損失を低減できる
ガソリンを燃料とするレシプロエンジンでは、燃焼エネルギーのうち、最大でも約40%しか動力として利用されていない。実に半分以上のエネルギーは出力以外で失われているのだ。この損失のうち、燃焼室やピストンの壁面から逃げる熱は「熱損失」と呼ばれる。
今主流の環境負荷低減思想のエンジンでは、この“熱損失”の低減が大きな課題となっている。この課題の解決には、熱が逃げる壁面積を減らすことが有効であり、その手段として気筒数の削減が挙げられる。
また、レシプロエンジンは、ピストン、コンロッド、クランクシャフト、カムシャフト、バルブまわりなど多くの稼働パーツで成り立っている。それらが稼働する際には、摩擦によるフリクションロスが発生する。このロスは、燃焼エネルギー全体の十数パーセントにも達し、出力のみでなく燃費への影響も大きい。
このフリクションロスは、当然のことながら稼働部品が少なく、パーツ同士の接触面積が少ないほど低減できる。この点でも、エンジンの気筒数を減らすことが有効である。
排気干渉を回避できる
燃焼をエネルギーに換えて出力を得るレシプロエンジンでは、燃焼に伴う振動を抑えることが大きな課題となっている。それには燃焼の間隔をうまく設定して、燃焼気筒同士の振動を打ち消し合うように設計することが最も合理的である。
これまで、これを効率よく実現できる最低気筒数は4気筒で、3気筒はバランスが良くないとされてきた。しかしその一方で、4気筒は振動を打ち消し合うための燃焼間隔から、“排気干渉”が起こるという問題を抱えている。
これは、ある気筒が排気をおこなおうとバルブを開いたときに、先に排気をおこなっていた他の気筒の排気圧力波が排気管を通して伝わり、スムーズな排気を妨げてしまうというもの。これは、常に2気筒ずつが同じ動きをする180度位相の直列4気筒エンジンの構造上の宿命であり、排気圧で過給するターボエンジンでも問題となっているため、排気経路での工夫が必須となっている。
その点、位相が270度で各気筒の動作タイミングが重ならない直列3気筒エンジンでは、この“排気干渉”が起こらない。なので排気経路に特別な工夫を施す必要がなく、排気経路が自由に設計できる。例えばターボチャージャーをシリンダーヘッドに直接装着するということも可能になる。
低回転トルクが増せる
エンジンのトルクは燃焼のエネルギーの大きさに左右される。総排気量が同じ1600ccだとして考えた場合、4気筒では1気筒あたりの排気量は400ccで、3気筒では約533ccとなり、単純計算で1.3倍の燃焼圧が得られることになる。
馬力は時間当たりの仕事率なので回転を上げれば高められるが、トルクは気筒あたりの排気量が大きい方が有利となる。
エンジンのコンパクト化
直列4気筒と直列3気筒を比べると、仮に排気量が同じなら、ボアの広さで多少大きくなるものの、気筒数が1つ少ない直列3気筒の方が、エンジン全長を大幅に短縮できる。
これはエンジンのレイアウトの自由度が向上することになり、スポーツ性能を追求するモデルでは大きなメリットとなる。
直列3気筒エンジンのデメリット
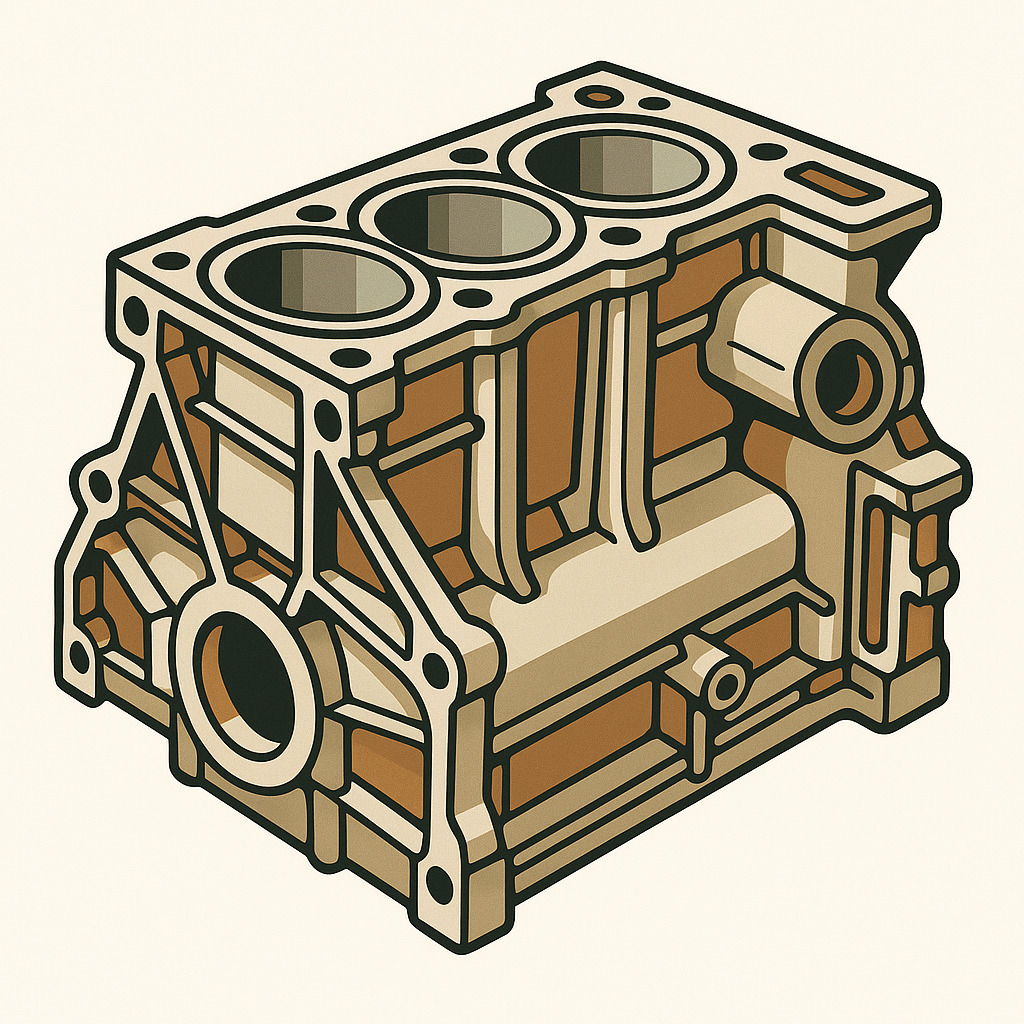
メリットがあればデメリットもある。ここでは直列3気筒エンジンのデメリットを挙げていこう。
振動が大きくガサツな印象になる
先に燃焼間隔について触れたが、燃焼による振動を気筒同士で打ち消せる最低気筒数は4気筒だ。3気筒は各気筒が240度の位相で連続して動いているため、燃焼の振動を互いに打ち消すことができない。
バランサーという重りで全体の振動をある程度抑えることは可能だが、クランクの回転に応力が加わるため、エンジンが斜めに回ろうとする動きが発生し、それが振動として現れる。コストを掛ければ4気筒と同等に抑えることも可能かもしれないが、3気筒エンジン搭載車種は低価格帯に多く採用される傾向があるため、現実的ではない。
気筒数=上等というイメージに対して不利
単純に気筒数が多いほど上等だという固定概念は、今でも根強く存在している。そのため、悪い言い方をすると「3気筒エンジンは安っぽい」というイメージを持つ人が多いとされ、採用に慎重になるケースも少なくないようだ。
直列3気筒エンジンを採用している車種の例
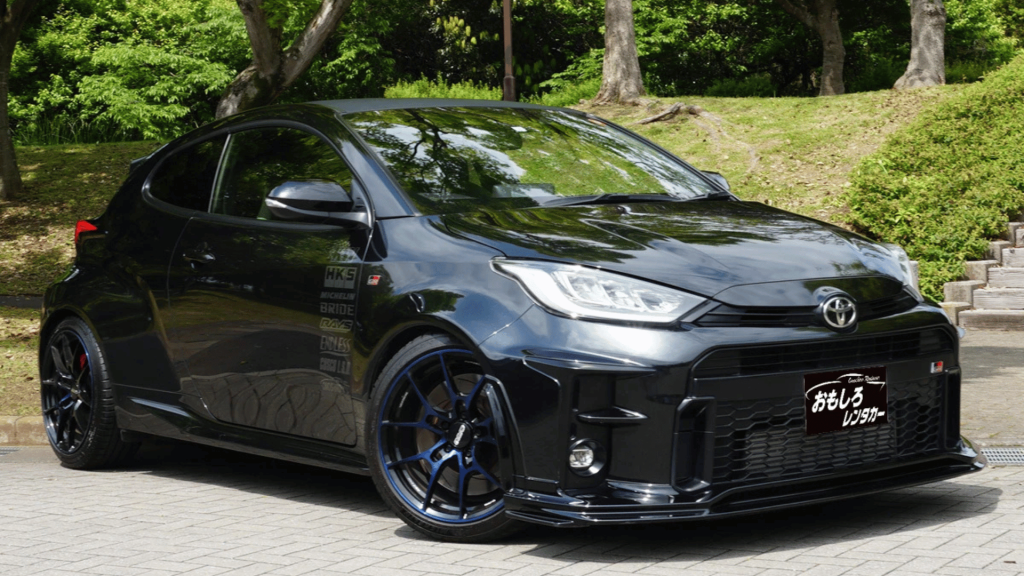
トヨタ・ヤリス
現行のヤリスでは、1.0リットルの「1KR」と、1.5リットルの「M15A」の2種のエンジンが用意されている。「1KR」はベースグレード用の小排気量タイプということで、低コスト、コンパクトという理由で直列3気筒が採用されていると思われる。
注目は1.5リットルの「M15A」。こちらは新開発のエンジンで、これまでなら1.5リットルクラスは直列4気筒を採用されていたが、あえて3気筒で新開発された。3気筒を選んだ理由のひとつはコンパクトな点。とりわけエンジン高を抑えられるという点は、ボンネットを低くできるというデザイン面にも有効だ。
そしてエネルギー効率を現在の最高レベルである40%を達成するため、熱損失とフリクションロスの低減に有効で、排気効率も良い3気筒を選んだとのこと。
フォルクスワーゲン・ポロ
現在では主流になったと言っても過言ではない“ロープレッシャー・ターボ・エンジン”の先駆けとなった直列3気筒エンジンを搭載したのが、VWのポロだ。登場は2011年。それまでは出力の向上に主眼が置かれていたターボチャージャーを、発想を大胆に変えて燃費向上のために用いた画期的なモデル。
トルクの立ち上がりが良く、排気干渉もないため、ロープレッシャー・ターボとの相性は抜群で、先駆けながらも高い完成度を誇り、以後のエンジン史における重要なマイルストーンとして刻まれている。
ホンダ・N-ONE
製造コストの低さと環境性能への相性の良さから、今では軽自動車のほぼすべてに直列3気筒エンジンが採用されている。その中でも比較的高い評価を得ているのが、「ホンダ・N-ONE」などに搭載されている「S07B型」エンジンだ。
環境問題が深刻化していた2017年に登場しただけに、開発の主眼はエネルギー効率の追求に置かれている。特徴的なのは、その手法が“超ロングストローク”という点。ロングストローク化は燃焼室を小さくできるので、燃焼速度が高められ、燃焼の熱損失が抑えられる。
そして熱損失が少ないということは、排気に回るエネルギーも大きいため、ターボチャージャーの過給効率も高まる。それを極めるため、ストローク/ボア比を常識外の1.293まで追い込んでいる。軽自動車のエンジンにもコストをしっかりとかけて開発しており、エンジン屋ホンダの面目躍如である。
直列3気筒エンジンは、燃費性能と軽快な走りを両立させる現代的な選択肢である。とはいえ、そのフィーリングや加速感は、スペックだけでは把握しきれない部分も多い。
もしその実力を確かめたいのであれば、「おもしろレンタカー」で実際に運転してみることをおすすめする。走行フィールやエンジンの鼓動を体で感じることで、3気筒エンジンの魅力をより深く理解することができるだろう。